Process of hot-dip galvanizing

We carry out the service of hot-dip galvanization in accordance with the standard ISO 1461 – Hot dip galvanized coatings on fabricated iron and steel articles.
In accordance with this standard, we can galvanize all steel elements that fit into our baths and are appropriately technologically prepared for hot-dip galvanizing.
Maximum allowed dimensions of articles for hot-dip galvanizing:
Dimension (max): 12,6 x 1,7 x 2,9 m
Weight (max): 7.000 kg
There are three phases of construction preparation:
- Openings for ventilation of closed parts and pockets
- Surface without paint and residue of previous surface protection
- Clean and non-porous welds.
Technological process includes four main phases:
1 |
Loading phase
In this phase, the articles are hung on special beams with wires or chains. Throughout the procedure, the loaded beams are transported with hoists. |
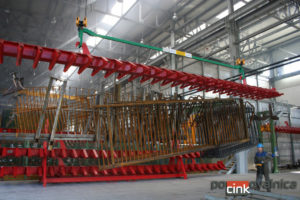 |
2 |
Chemical cleaning and pretreatment
The hung articles are cleaned of rust and scalings by dipping in chemical baths. The articles are then degreased in acidic degreaser, followed by leaching in hydrochloric acid. When cleaned, the articles are rinsed in water, dipped in a flux solution and then dried in a drying chamber. |
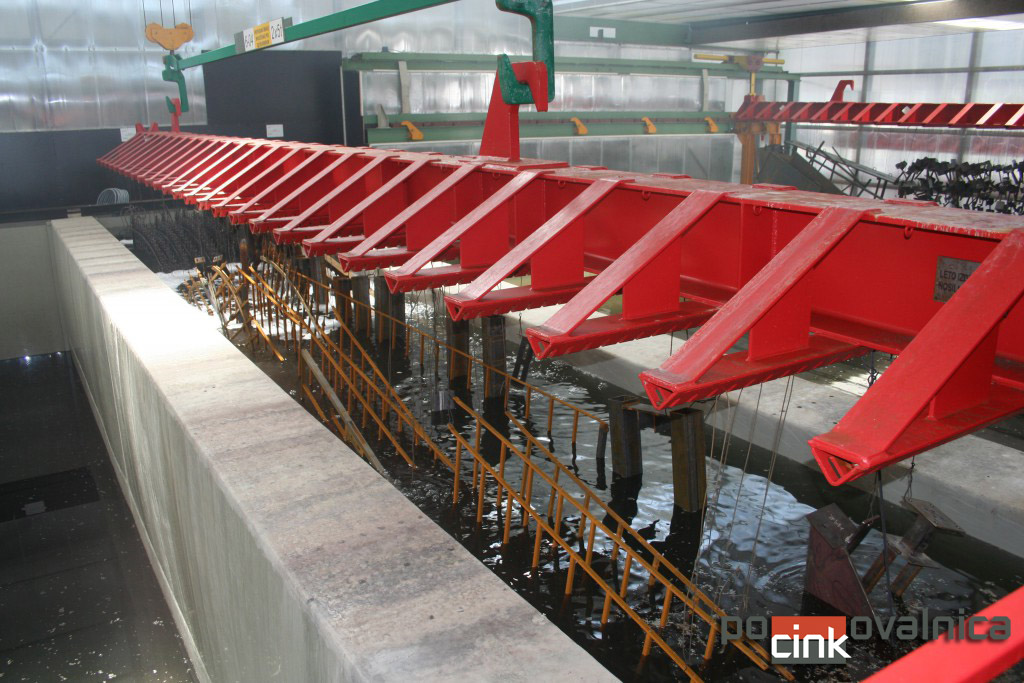 |
3 |
Hot-dip galvanizing in molten zinc
Prepared articles are then dipped in molten zinc. During this procedure, a metallurgical binding of zinc and iron occurs.
If needed, elements are cooled in water. |
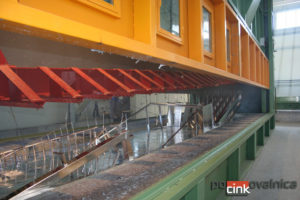 |
4 |
Unloading, cleaning and packaging
The final phase consists of unloading, cleaning of zinc residue and zinc ash, and packaging.
Finally, the parcel is weighed and stored at a terminal, where it awaits dispatch. |
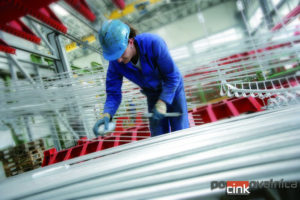 |